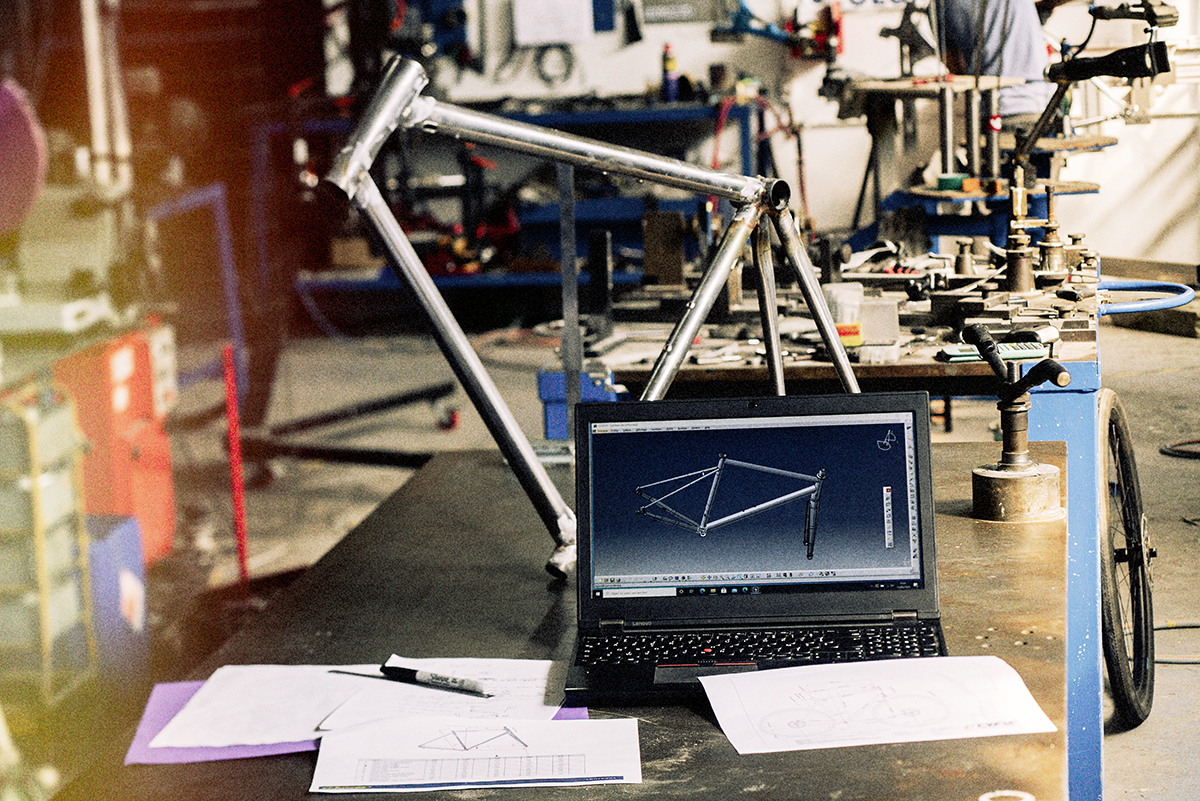
Des produits uniques,
qui vous ressemblent
Chaque produit est fabriqué à la main avec exigence et passion dans la plus pure tradition artisanale.
La fabrication s’inscrit dans la modernité avec des matériaux et techniques les plus élaborés et une finition de qualité. Nous fabriquons en petites séries avec le souci du détail et de la perfection.
Chaque cadre est numéroté, unique et personnalisable.
Et c’est parce que vous êtes unique à nos yeux que vous avez la possibilité de choisir votre couleur, d’apposer votre nom ou vos initiales sur votre cadre si vous le souhaitez. Vous pourrez suivre les différentes étapes de la réalisation de votre cadre et voir le montage de votre vélo si vous choisissez un vélo numéroté DILECTA.
Une fabrication artisanale
« Made in France »
Nous sélectionnons les meilleurs matériaux dans chaque catégorie avec leurs caractéristiques mécaniques propres. Que ce soit alliage d’aciers sur nos modèles Le Blanc ou Forçat ou fibres de carbone demain, ils sont associés à des techniques de fabrication traditionnelle garantissant confort, rendement, durabilité, légèreté sans négliger la performance.
Nous avons choisi l’acier haut de gamme de la célèbre marque italienne Colombus : le SPIRIT HSS, très fin, très léger, extrêmement confortable sans jamais sacrifier le rendement qui offre de multiples options de customisation. Nous vous laissons le choix de l’intégration des gaines ou non.
Process de fabrication
du cadre
Chaque tube qui compose votre cadre est d’abord usiné en machine selon sa géométrie.
Nous réalisons nos découpes avec une précision extrême, une tolérance au dixième de millimètre sur un gabarit d’assemblage.
Puis, nous relions les tubes les uns aux autres par une technique de soudo-brasure, un apport de métal et une température de fusion qui permet de solidariser et consolider le cadre lors de cette première étape.
Le passage du cadre sur le marbre nous permet de contrôler l’alignement exact des tubes.
Le cadreur réalise le soudo-brasage définitif des tubes en suivant une séquence spécifique qui assure la stabilité dimensionnelle et la cohérence de l’ensemble.
Le passage du cadre sur le marbre permet de contrôler l’alignement exact des tubes.
Victor et Damien, ateliers Cyfac
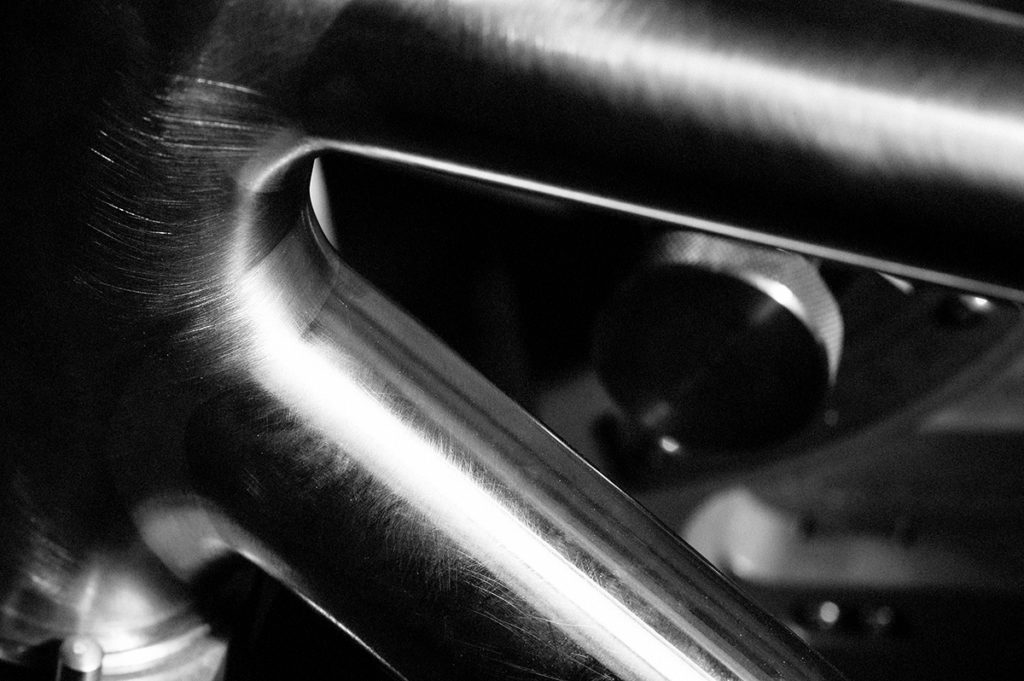
Tous les cordons de soudure font l’objet d’un polissage manuel
Cette étape -plus de 4 heures de travail par cadre- permet de supprimer le phénomène de concentration de contrainte. Lorsque le cordon est parfaitement poli, la contrainte se diffuse de façon homogène et le cadre gagne en solidité et en efficacité.
Une fois votre cadre soudé, nous le faisons passer 3 heures dans un bain de cataphorèse pour garantir le traitement anti-corrosion.
Toute la surface de la pièce est couverte, y compris les parties creuses et cachées ainsi que les arêtes vives. L’homogénéité de la couche confère une excellente tenue à la corrosion et une bonne couche d’accroche pour un primaire qui va suivre.
Peinture
Nous vous proposons un panel de couleurs au choix :
16 couleurs différentes sont proposées pour chacun de nos modèles que vous pouvez découvrir et tester sur notre configurateur couleurs. Nous utilisons des peintures écologiques dont le procédé ne fait plus appel aux solvants chimiques. Elles sont respectueuses de l’environnement et de la santé de nos artisans. Elles offrent une finition unique et précise.
Au total, il faut environ 20 heures pour fabriquer un cadre à la main dans la plus pure tradition artisanale dont 4 à 5 heures de polissage pour la finition.
Pour en savoir plus
Ils roulent Dilecta
Découvrez nos vélos
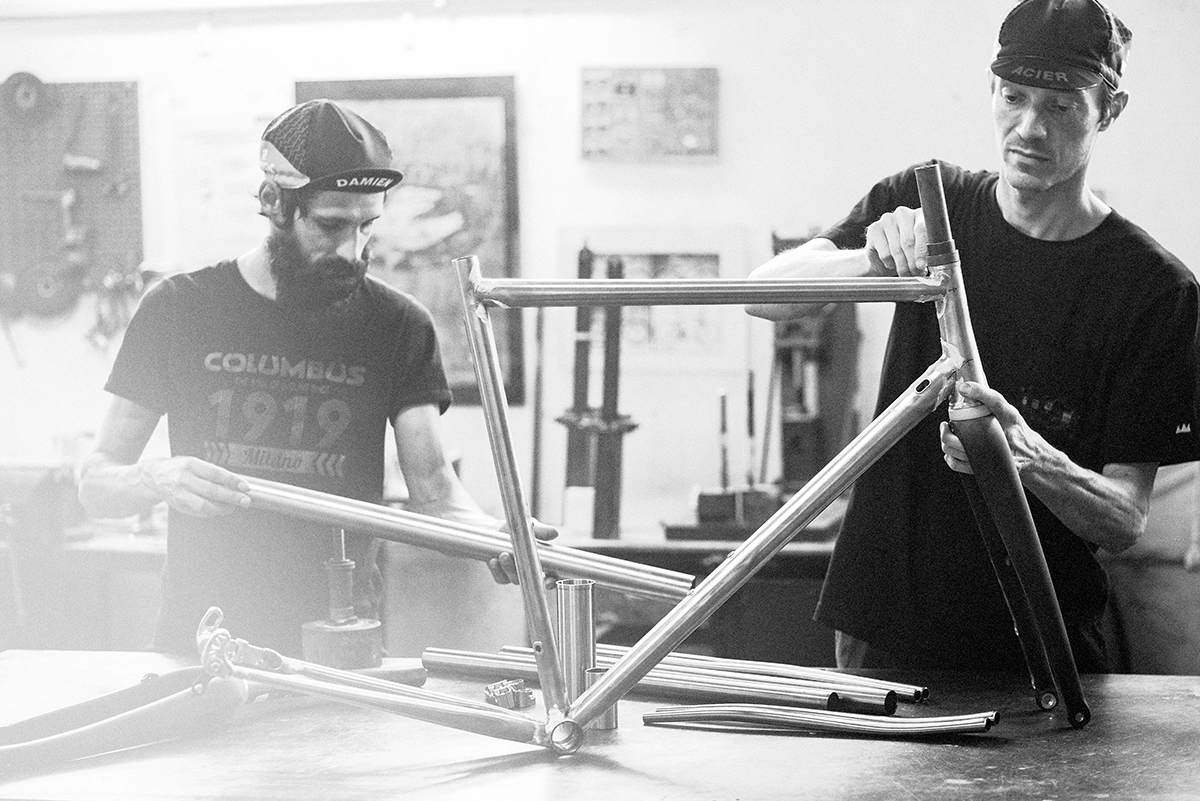
Délais de fabrication